All at sea.
As you know, we only rescue fruit and veg from abroad if it arrives in the UK by sea. But while having a no air-miles policy is much better for the planet, it does throw up its share of challenges – as we’ve explored in our recent box letters.
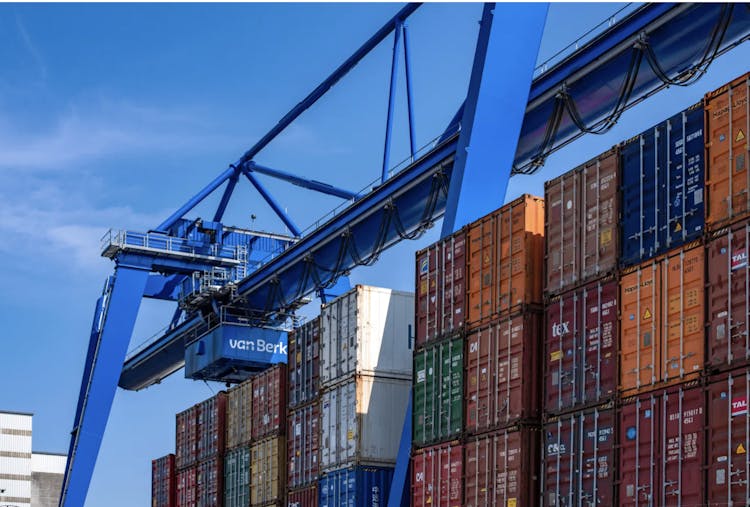
Spend a day with our sourcing team and you’re guaranteed to have a headache pretty quickly. Multiple box types to fill with rescued fruit and veg from all over the world arriving at different times and with different shelf lives and storage needs… where do you even begin?
But while Bels and her team are well-placed to manage the complex logistics and day-to-day hiccups along the way, the past few months have seen all kinds of shipping issues that no one could predict.
Storms at sea
The weather plays a huge part when it comes to the shipping of fresh food – both before it reaches the port and once it sets sail. It was so rainy in Brazil earlier this year that fruit and veg was delayed on its journey, having travelled by road from farms.
And then once everything arrives, bad sailing conditions and other issues can delay ships leaving ports, meaning they then arrive late at every stop along their journey. Cape Town is a microcosm of this situation, with problematic equipment, staffing shortages and difficult windy weather all impacting goods leaving the port over recent months.
Once containers get delayed, there’s a knock-on effect for others and backlogs can pile up. Not only are containers reaching destinations late, they’re then having to join a queue of items waiting to enter the country and be unpacked – it’s a vicious cycle!
And then there’s been the conflict in the Red Sea. Around a third of all global container shipping flows through there, which means commercial freighters have had to change routes to stay safe. This takes lots of planning, and increased fuel and administrative costs – all of which delays their journeys.
All this is just the tip of the iceberg – other recent issues we’ve come up against include produce getting stopped for inspection just as it arrives in the UK, along with lots of delays at UK ports and border controls post-Brexit. To call it unpredictable would be the understatement of the century.
Bels at the helm
Predicting what time delayed fruit and veg will arrive can be a nightmare – not just for the people involved, but for food waste too. In all these instances, Bels and her team have had to find a replacement item at short notice – or make sure the fruit is packed immediately upon arrival, with an eye on its shelf life.
They’re also faced with the challenge of delayed items suddenly all arriving at once, like the Egyptian spring onions we rescued recently. Thanks to disruption on route, multiple ships bunched up, all reaching the UK at once. Suddenly, there was a lot more supply than demand – without Oddbox, thousands of kilos would likely have gone to waste.
So how does the sourcing team manage it? And just how much time can you spend tracking ships in one day? Well, to start with, if there’s any chance something won’t reach us in time to go in your box, we’ll always have a replacement lined up so you aren’t left with a lack of lemons – this is why you might spot an ‘either/or’ listing on your box contents list.
We’re also always ready to change our rescue lists (and add-ons) if anything makes a surprise appearance. One of our melon suppliers recently received 126 containers in one day having had nothing for three weeks – needless to say, we rescued a lot more melons that week than planned.
This level of flexibility has been praised by our UK growers, but it’s been more important than ever recently for supporting our overseas suppliers too. With a community of food waste-fighters like ours, we know we can weather the stormy seas, rescuing as much fruit and veg as possible – whenever it arrives and whatever it looks like. Who knows? It might even arrive in time for breakfast.